汽车尾门弹簧植绒生产线是专门用于对汽车尾门弹簧表面进行植绒处理的设备组合,通过该生产线处理后的弹簧,能降低工作时产生的噪音,提升尾门的使用体验,以下从生产线的组成部分、工作原理、特点等方面为你详细介绍:
-
生产线组成
上料系统:由放置台和自动上料装置构成。放置台用于存放待植绒的汽车尾门弹簧,自动上料装置通常配备有机械抓手或吸盘,能够精准地抓取弹簧,并按照设定的顺序和位置,将弹簧放置在输送轨道上,确保弹簧在后续加工过程中的准确传输。
预处理系统:包括清洗设备和干燥设备。清洗设备一般采用喷淋或超声波清洗的方式,去除弹簧表面的油污、杂质和氧化层,为植绒提供良好的表面基础。干燥设备则利用热风或真空干燥等技术,迅速将清洗后的弹簧表面的水分去除,防止水分影响植绒效果。
植绒系统:这是整个生产线的核心部分,主要由植绒机、绒毛供给装置和静电发生器组成。植绒机是实现植绒操作的关键设备,它通过静电场的作用,使绒毛在电场中带电并垂直飞向弹簧表面。绒毛供给装置负责均匀地向植绒机输送绒毛,确保绒毛的供应稳定。静电发生器则产生高压静电场,为绒毛的飞行提供动力,使绒毛能够牢固地附着在弹簧表面。
胶水涂覆系统:由胶水储存罐、涂胶泵和涂胶头组成。胶水储存罐用于储存适合弹簧植绒的专用胶水,涂胶泵将胶水从储存罐中抽出,并通过涂胶头均匀地涂覆在弹簧表面。涂胶的厚度和均匀性可以通过调节涂胶泵的流量和涂胶头的移动速度来控制,以保证绒毛能够充分地与胶水接触并牢固附着。
固化系统:通常采用隧道式烘箱或热风循环固化炉。经过植绒的弹簧通过输送轨道进入固化系统,在一定的温度和时间条件下,胶水发生固化反应,使绒毛与弹簧表面牢固结合。固化温度和时间可以根据胶水的特性和弹簧的材质进行精确调整,确保植绒效果的稳定性和可靠性。
后处理系统:包括修剪设备和清洁设备。修剪设备用于去除弹簧表面多余的绒毛,使植绒表面更加平整、美观。清洁设备则通过吸尘或吹扫等方式,清除弹簧表面残留的绒毛和杂质,保证弹簧的清洁度。
下料及检测系统:下料系统由下料机械手臂和成品放置台组成,机械手臂将经过后处理的弹簧从生产线上取下,并放置在成品放置台上。检测系统则利用光学检测设备和力学检测设备,对弹簧的植绒质量进行检测,包括绒毛的附着牢度、植绒的均匀性、弹簧的力学性能等指标,确保产品符合质量标准。
工作原理:汽车尾门弹簧首先通过上料系统进入生产线,经过预处理系统清洗和干燥后,由胶水涂覆系统在弹簧表面均匀涂覆胶水。随后,弹簧进入植绒系统,在静电场的作用下,绒毛垂直飞向弹簧表面并附着在涂有胶水的部位。接着,带有绒毛的弹簧进入固化系统,使胶水固化,将绒毛牢固地固定在弹簧表面。经过固化后的弹簧再进入后处理系统进行修剪和清洁,最后由下料及检测系统进行下料和质量检测,合格的产品进入成品库,不合格的产品则进行返工处理。
生产线特点
自动化程度高:从弹簧的上料、预处理、植绒、固化到后处理和检测,整个过程实现了高度自动化,减少了人工干预,提高了生产效率和产品质量的稳定性。
植绒质量好:通过精确控制胶水涂覆量、植绒时间和静电场强度等参数,能够保证绒毛均匀、牢固地附着在弹簧表面,植绒效果良好,有效提升了弹簧的性能和品质。
生产效率高:生产线采用连续作业的方式,能够快速地对大量汽车尾门弹簧进行植绒处理,满足汽车制造业大规模生产的需求。
灵活性强:可以根据不同型号和规格的汽车尾门弹簧,通过调整设备参数和更换模具等方式,实现多样化产品的植绒生产,具有较强的适应性。
环保节能:采用先进的植绒技术和环保型胶水,减少了有害气体的排放和环境污染。同时,生产线在设备设计和运行过程中注重节能,降低了能源消耗。
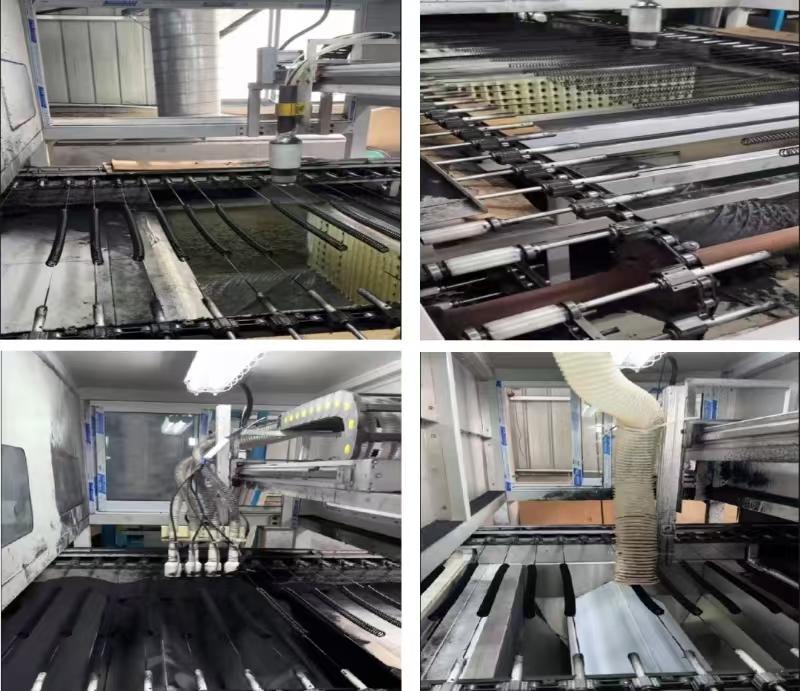